Marcus Spangler, kierownik badań i projektów Warwick i Framus, jest jednocześnie głównym konstruktorem i szefem produkcji. To człowiek odpowiadający bezpośrednio za jakość gitar sygnowanych logiem Warwick i Framus. Jeśli ktoś może nam szczegółowo opowiedzieć o całym procesie produkcyjnym, to właśnie on.
Co dokładnie należy do twoich obowiązków w Warwicku i Framusie? Można nazwać cię głównym projektantem? Nadzorujesz cały proces projektowania i produkcji?
Opiekuję się wszystkim, czym zajmują się Warwick i Framus, oczywiście wspólnie z moim zespołem produkcyjnym. Pracując drużynowo, zajmujemy się także planowaniem nowych modeli, jeśli chodzi o design i wdrażaniem ich do produkcji. Oczywiście we wszystko jest też zawsze zaangażowany Hans-Peter Wilfer.
Warwick produkuje bardzo dużo modeli. Czy da się usystematyzować wszystkie serie, które obecnie są produkowane pod szyldem Warwicka?
Mamy trzy główne linie, a w ramach każdej z nich różne modele i kształty. Modele Rockbass są projektowane i opracowywane od inżynieryjnej strony w Niemczech, ale produkowane w Chinach. Seria Teambuilt powstaje w Niemczech. Mamy tutaj mniej możliwości modyfikacji, przez co jesteśmy w stanie produkować nieco większe ilości tych instrumentów, co z kolei pozwala na obniżenie ich cen. Jest też rzecz jasna seria Masterbuilt Customshop, gdzie praktycznie wszystko jest możliwe, a każdy instrument jest dziełem sztuki. Jak w naszym sloganie: „Jeśli możesz to wymarzyć, my możemy to zbudować”!
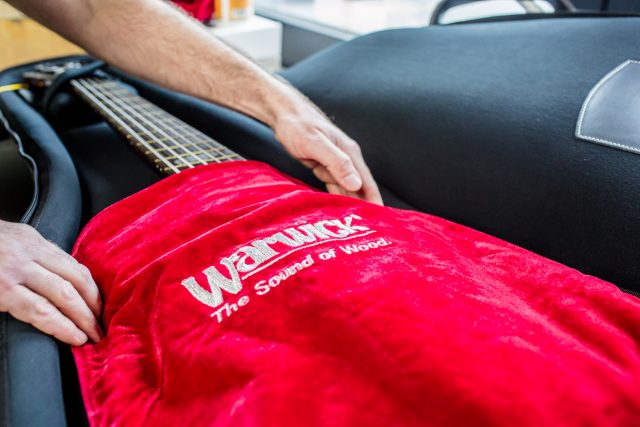
Możesz określić, które z pomysłów i patentów, jakie Warwick i Framus wprowadziły w swoich instrumentach na przestrzeni lat, były najważniejsze?
Było ich mnóstwo… Począwszy od łatwo dostępnego pręta napinającego i pokrywy komory z elektroniką, przez laminację szyjki i wzmocnienie wyżłobienia w gryfie, po dwuczęściowy mostek Warwick 3D i oczywiście duży wachlarz egzotycznego drewna. Jesteśmy też dumni z niewidzialnego systemu nabijania progów i naszego unikalnego systemu lakierowania UV.
Warwick i Framus mają wyjątkową linię produkcyjną. Czym się wyróżnia? Jaka jest największa korzyść, jaką odnosicie dzięki niej?
Zawsze zwracamy uwagę na to, co jest najkorzystniejsze dla instrumentu i oczywiście dla samego muzyka. Trzeba zdawać sobie sprawę, że pewne detale mogą być doprowadzone do perfekcji wyłącznie za pomocą super precyzyjnych maszyn kontrolowanych przez komputery. Z kolei inne rzeczy da się wykonać w sposób doskonały tylko i wyłącznie przez człowieka o odpowiednich umiejętnościach. Wszystko to trzeba zbilansować, by zyskać idealny produkt.
Który z modeli basów Warwicka jest najbardziej popularny i dlaczego?
Jeśli nie mówimy o twardych liczbach i wynikach sprzedaży, to powiem, że dla mnie jest to Buzzard zaprojektowany przez Hansa-Petera i Johna Entwistle’a. Może nie każdy ten instrument kocha, ale na pewno każdy basista, który gra lub interesuje się rock and rollem go kojarzy… Dla mnie jest to jeden z najlepiej zaprojektowanych instrumentów w historii rock and rolla i gitar basowych.
Lata temu Warwick posługiwał się sloganem „brzmienie drewna”. Jaka jest dziś filozofia brzmienia w Warwicku i Framusie?
Wciąż taka sama. Drewno to w dalszym ciągu najważniejsza część instrumentu, nawet jeśli go nie dostrzegasz pod porządnym lakierowaniem. A typowe brzmienie Warwicka pochodzi głównie z drewna.
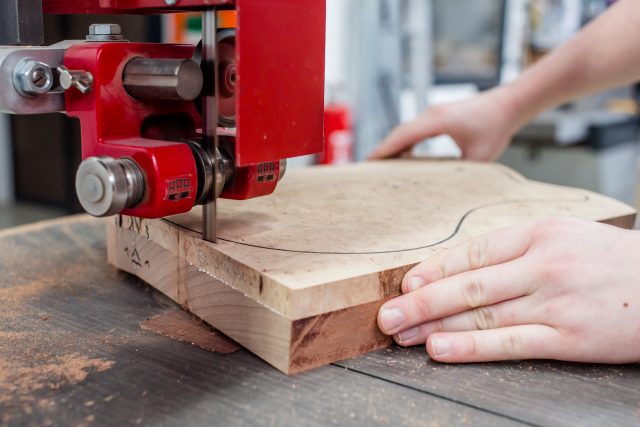
Spójrzmy w przeszłość raz jeszcze: czy przeciętne wymagania gitarzystów i basistów w stosunku do ich sprzętu się bardzo zmieniły? Czy to dziś duże wyzwanie – dostarczyć im instrument, który sprosta ich wymogom?
To zależy – niektórzy artyści są bardziej „oldschoolowi” i pozostają przy tradycyjnych specyfikacjach. Inni, przede wszystkim młodzi, są bardziej otwarci na nowinki i chcą ich wszystkich wypróbować. Mówiąc ogólnie, zawsze największym wyzwaniem jest określić, czego dokładnie dany artysta chce i potrzebuje.
Która z gitar Framusa jest obecnie najnowocześniejsza i najbardziej zaawansowana technicznie? Model Devina Townsenda należy do takich?
Bez wątpienia gitara Devina pod względem stylistyki i technicznych specyfikacji jest jedną z najnowocześniejszych na rynku. Wyróżnia się też sposobem budowy i tego, jak jest produkowana od strony technicznej – inaczej niż zwykłe gitary o tym przekroju. Wyzwaniem w produkcji są też gitary Idolmaker. Gdybyśmy nie posiadali odpowiedniej wiedzy i maszyn, które same w sobie są technologicznymi dziełami sztuki, nie bylibyśmy w stanie produkować ich w odpowiedniej jakości.
Wiem, że modele sygnowane przez artystów są bardzo ważne dla wizerunku firmy. Jakie są twoje doświadczenia z pracy z gwiazdami? To przyjemność czy tortura?
Dla mnie praca z artystami to zawsze przyjemność, nawet kiedy bywa upierdliwa. Ale zawsze jest to dobra zabawa, a przy tym nauka i wyzwanie, bo tworzysz coś zupełnie nowego. Nad takimi modelami pracujemy z artystami ramię w ramię. Robimy szkice i projekty, wysyłamy, dostajemy jakieś poprawki i sugestie… Krok po kroku nowy instrument wyłania się z bardzo ogólnych szkiców i niezgrabnych prototypów.
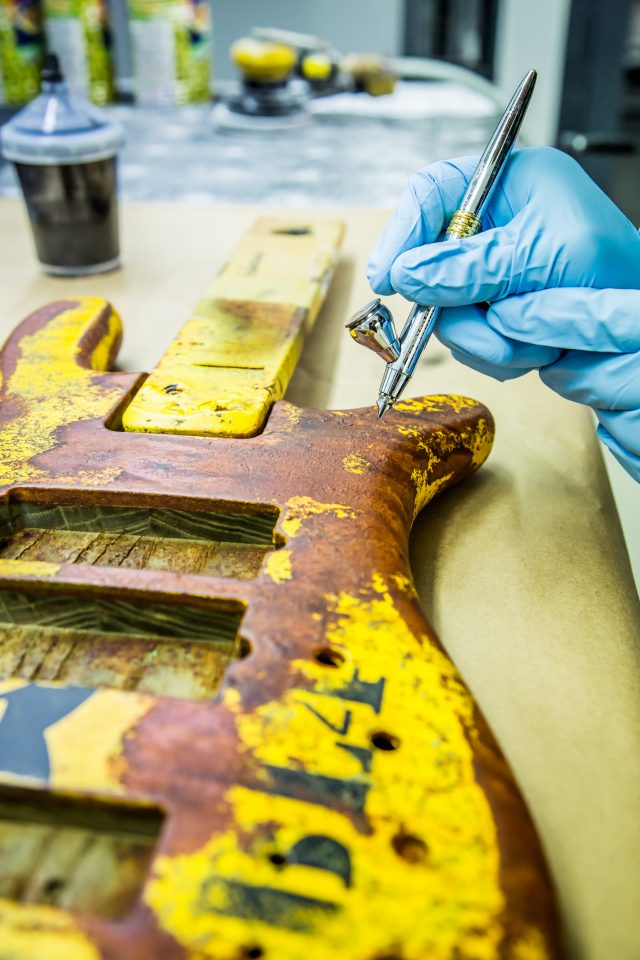
Jaki jest najtrudniejszy moment w całym procesie tworzenia nowego instrumentu, punkt krytyczny dla każdych nowych idei?
Najtrudniejsze jest opracowanie wszystkich detali, kiedy gotowy jest już design instrumentu. Czasami gitara wygląda świetnie i wszystko działa, a potem okazuje się na przykład, że jest źle zbalansowana albo nie mamy części o odpowiednim rozmiarze, albo jeszcze, że te części, które mamy, będą wyglądały naprawdę źle i trzeba zrobić jakieś od nowa. Największym wyzwaniem jest pozbierać to wszystko do kupy.
Co to znaczy, że cały proces produkcyjny jest „zielony”? Jak być eko przy produkcji gitar?
Zaczyna się od surowych materiałów. Sprawdzamy każde źródło, z którego je zamawiamy. Upewniamy się, że lasy, z których pochodzi nasze drewno, są podtrzymywane, są nowe nasadzenia. Potem jest energia – produkujemy ją w znakomitej większości sami. Staramy się jej wytwarzać ile się da. Pozyskujemy prąd z energii słonecznej, wiatru, źródeł geotermalnych i naszej własnej elektrowni. Wszystkie światła są wyposażone w czujniki, więc na przykład wyłączają się same, gdy nikogo nie ma w pomieszczeniu. Czasami, kiedy odwiedzają nas goście, odnoszą wrażenie, że produkcja stoi, że nikogo nie ma w fabryce, bo wszystkie światła są pogaszone, ale prawda jest taka, że wyszkoliliśmy nasz zespół, by włączał je tylko tam, gdzie to konieczne i tam, gdzie ktoś pracuje. Przyzwyczailiśmy się nawet do wyłączania światełek czuwania w sprzętach elektronicznych i monitorach komputerów, choć wydawałoby się, że to nic nie znacząca sprawa. Widzisz więc, że poczynając od samych surowych komponentów, kończąc na funkcjonowaniu firmy, robimy wszystko, by wszystko było jak najbardziej zielone i eko.
Zakup magazyn z wywiadem tutaj.